1.本发明涉及数控机床状态监测技术领域,尤其涉及一种基于多源参数的数控机床数据格式规范化处理方法。背景技术:2.目前,数控机床加工精度高,自动化程度高,是制造业至关重要的基础支撑装备,多源参数同步采集的数据集格式规范化处理对于数控机床的状态监测与故障诊断具有重要意义。数据采集是利用传感器从系统外部采集待测设备数据并输入到系统内部的接口中,然后在上位机中分析、处理的过程。所采集的数据是已转换为电信号的各种物理量,可以是模拟量,也可以是数字量,数据采集系统是集成基于计算机或者其他专用测试平台的测量软、硬件实现灵活的、用户自定义的测量系统。3.对数控机床进行状态监测或者故障诊断时,需要采集的数据往往多种、多源,包括基于应变原理的切削力、振动、微位移、功率、温度等多源参数,每种参数形成若干数据集,如何将这些不同的类型传感器、不同模态、不同频率的数据集进行规范化使各网络能接收,并在上位机中处理,并上传至网络一直是行业亟待解决的难点问题。技术实现要素:4.本发明的目的是提供一种基于多源参数的数控机床数据格式规范化处理方法,该方法能够确保在数控机床同一工况下采集到所需的多源多种数据集,并对所采集的数据进行设定的规范化格式处理,便于多源信号在上位机中分析处理,提高处理效率。5.本发明的目的是通过以下技术方案实现的:6.一种基于多源参数的数控机床数据格式规范化处理方法,所述方法包括:7.步骤1、使用多源传感器同步采集同一工况下数控机床的多源参数;所述多源参数包括工件受到的切削力信号、工作台的振动加速度信号、微位移信号、机床的功率信号、加工环境的温度信号;8.步骤2、将所采集的并经过放大处理后的多源参数信号通过usb、pci、以太网总线接入嵌入式系统中,由嵌入式系统对多源参数信号进行幅值、无量纲化、归一化、数据校准四个层级的处理,如果国宝会说话解说词将信号转变为规范化格式;9.步骤3、再将规范化格式处理后的信号数据通过工业以太网交换机传输至上位机,由所述上位机进行数据分析处理,判断所述数控机床的状态或存在的故障。10.由上述本发明提供的技术方案可以看出,上述方法能够确保在数控机床同一工况下采集到所需的多源多种数据集,并对所采集的数据进行设定的规范化格式处理,便于多源信号在上位机中分析处理,提高处理效率。附图说明11.为了更清楚地说明本发明实施例的技术方案,下面将对实施例描述中所需要使用的附图作简单地介绍,显而易见地,下面描述中的附图仅仅是本发明的一些实施例,对于本领域的普通技术人员来讲,在不付出创造性劳动的前提下,还可以根据这些附图获得其他附图。12.图1为本发明实施例提供的基于多源参数的数控机床数据格式规范化处理方法流程示意图;13.图2为本发明实施例所述多源参数采集的过程示意图;14.图3为本发明实施例所述数据校准的过程示意图。具体实施方式15.下面结合本发明实施例中的附图,对本发明实施例中的技术方案进行清楚、完整地描述,显然,所描述的实施例仅仅是本发明一部分实施例,而不是全部的实施例,这并不构成对本发明的限制。基于本发明的实施例,本领域普通技术人员在没有做出创造性劳动前提下所获得的所有其他实施例,都属于本发明的保护范围。16.如图1为本发明实施例提供的基于多源参数的数控机床数据格式规范化处理
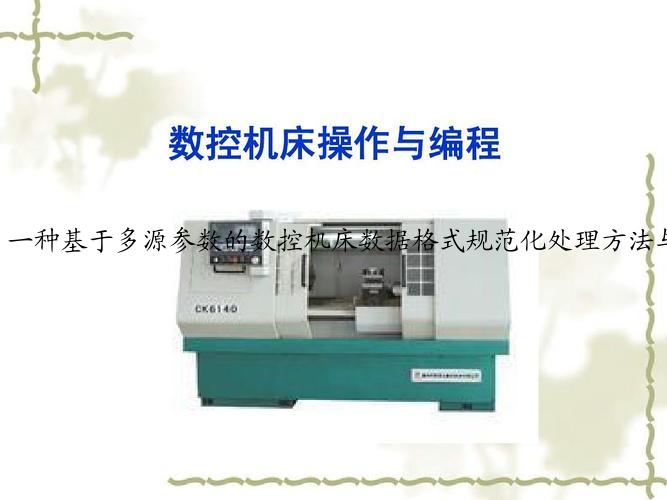
方法流程示意图,所述方法包括:17.步骤1、使用多源传感器同步采集同一工况下数控机床的多源参数;所述多源参数包括工件受到的切削力信号1i、工作台的振动加速度信号2i、微位移信号3i、机床的功率信号4i、加工环境的温度信号5i;18.其中,多源参数数据构成多源数据集,包括切削力(f)数据集、振动(v)数据集、微位移(d)数据集、功率(p)数据集和温度(t)数据集。19.在该步骤中,可以将多个用于采集多源数据的传感器安装在数控机床上,然后获取相应的数据,如图2所示为本发明实施例所述多源参数采集的过程示意图,图中包括切削力感知模块1i、振动加速度感知模块2i、微位移感知模块3i、温度感知模块4i、功率感知模块5i和基准触发信号感知模块6i,将多个用于采集多源数据的传感器(图中的切削力感知模块1i、振动加速度感知模块2i、微位移感知模块3i、温度感知模块4i、功率感知模块5i)安装在数控机床上,通过基准触发信号感知模块6i及其放大器106,将触发信号传输至全部数据采集单元201,202,203,204和205,触发各通道的传感器模块同步采集多源参数数据;20.切削力感知模块1i、振动加速度感知模块2i、微位移感知模块3i、温度感知模块4i、功率感知模块5i同步采集同一工况下数控机床的多源参数,并将采集的多源参数信号通过放大器101、102、103、104、105进行信号放大,减小在传输过程中信号衰减带来的影响;由于不同类型的传感器应用不同原理,每个传感器应该有与之类型相对应的信号放大器,例如压电式传感器需要配合电荷放大器使用;21.所述数据采集单元201,202,203,204和205再将放大后的多源参数信号转换成数字信号,以进行后续数据传输。22.具体实现中,数控机床的切削力是工件加工过程中最为关键的参数,机床的功率是后续分析计算中的重要指标,加工平台的微位移和加工环境的温度也是也会对工件的加工精度产生影响,本实施例中切削力数据获取方法采用一组三向切削力集成传感器单元,可同时测量三个方向的切削力,安装于工件与工作台之间。23.分析加速度信号一般是机械行业中进行振动测试时常用的典型方式,在数控机床工作台上安装三向压电式加速度传感器测试x、y、z三个方向的振动情况,即工作台的振动信号。24.工件工作台受压后产生的微位移和加工环境过热引起的工件变形均会对工件的加工精度产生影响。25.上述本实例所采集的数据集均是数控机床在同一工况下获取,保证了后续根据这些数据进行分析得到的机床多源参数同步采集结果可靠。26.步骤2、将所采集的并经过放大处理后的多源参数信号通过usb、pci、以太网总线接入嵌入式系统(如图2中的301、302、303、304、305)中,由嵌入式系统对多源参数信号进行幅值、无量纲化、归一化、数据校准四个层级的处理,将信号转变为规范化格式;27.由于本实施例的数据采集过程涉及多源传感器,有模拟量,也有数字量;有电压传感器,也有电荷传感器。它们所测试的原理和数据不同,所采集到的信号也具有不同的波形特点,如果未对这些数据进行规范化格式处理,它们在上位机中不能很好的显示,也不便于数据处理。28.故在该步骤中,由嵌入式系统301、302、303、304、305对多源参数信号进行幅值、无量纲化、归一化、数据校准四个层级的处理,将信号转变为规范化格式,这里数据集格式规范化处理的原理具体为:29.同步采集的第i通道的第j个时域数据表示为xij,表示第i通道,i=1,2,…
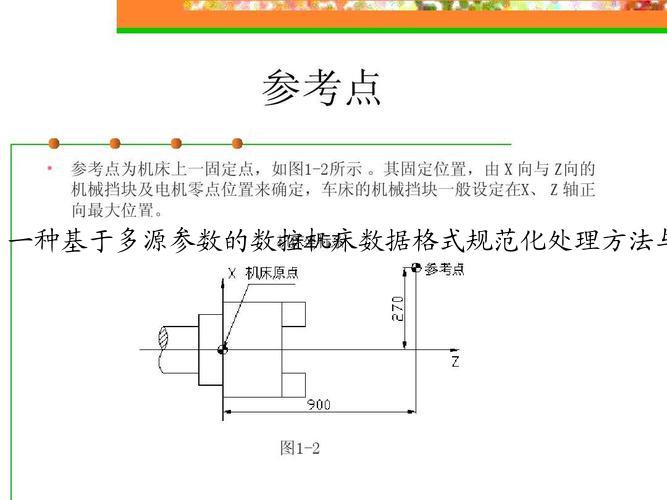
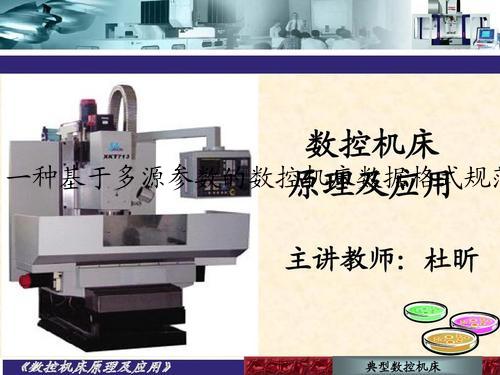
,m(总通道数);第j个时域数据,j=1,2,…,n(第i通道采集数据的数量)。在一定时间内,数控机床多源参数同步采集系统第i通道采集的所有数据集合称为数据集xi,即xi={xij,j=1,2,…,n};30.对于第i通道参数,计算n个数据的最大值和最小值及平均值:31.最大值:ximax=maxxi32.最小值:ximin=minxi33.平均值:34.为了防止因数据过大或过小而引入的计算误差,对最大值与最小值区段进行划分;同时在显示时,采用不同颜色的线条表示不同区段数据,也便于实现同框可视化。35.实时采集数据倍率及分区段描述,以数据相差10倍为基准,引入倍率系数ki表示(i=1,2,...,m)36.k1表示ximax最大值与最小值ximin相差10倍;37.k2表示最大值ximax与最小值ximin相差20倍;38.k3表示最大值ximax与最小值ximin相差30倍;39......以此类推。40.ki表示最大值ximax与最小值ximin相差i×10倍;41.km表示最大值ximax与最小值ximin相差m×10倍。42.根据ximin与ximax的差值,根据xij的幅值可分的区段数用m表示:43.m=mod(ximax/ximin)44.mod表示取整;采用进位制,小数圆整为整数,以免信息被截断。45.最大值ximax与任一参数xij的倍率为ki=mod(ximax/xij),则该参数可描述为:46.xij=ki×10i×xsijk,变换为:[0047][0048]这里,xsijk表示将时域数据xij按区段调理后,调理参数幅值均在[-10,10]区间。与此对应,采集时域数据集xi变换为调理数据集xsik,
数控机床配件大全下标中,s表示按区段调理数据,i表示第i通道。[0049]然后按区段倍率对调理数据无量纲化及归一化处理,具体取xsijk的最大值(绝对值)和最小值的绝对值,即:[0050]xsijkm=|max(xsijk)-min(xsijk)|[0051]无量纲化处理数据:[0052][0053]xcik表示分段无量纲化和归一化处理后的数据集,这里,xcik数据集的元素范围在[-1,1]区间。[0054]实时采集原始数据xij规范化处理后的值与无量纲化数据集xcik的变换关系,表示为:[0055][0056]其中,i=1,2,...,m;j=1,2,...,n;xcik为原始数据xij分段无量纲化和归一化的参数数据集。[0057]基于上述原理,由嵌入式系统对多源参数信号进行幅值、无量纲化、归一化、数据校准四个层级的处理,将信号转变为规范化格式的过程具体为:[0058]1)针对工件受到的切削力信号处理过程为:[0059]工件受到的切削力信号包括fx(n)、fy(n)、fz(n)3个通道的切削力参数,用xfij表示,单位n;这里i=1,2,3;i=1表示fx;i=2表示fy;i=3表示fz,对应3个通道;j表示任意采样点的测量分力,j=1,2,...,n;[0060](1)首先计算3个通道切削力数据最大值、最小值及绝对值[0061]对3个通道切削力分量进行描述,xf1j表示fx;xf2j表示fy;xf3j表示fz,由于采用基准触发信号,三个方向的切削力量纲一致,具备无量纲化条件,横向进行无量纲化处理;[0062]最大值xfimax=max[max(xfij,j=1,2,...,n),i=1,2,3][0063]最小值xfimin=min[min(xfij,j=1,2,...,n),i=1,2,3][0064]绝对值xfmax=max[|xfimax-xfimin|][0065](2)实时采集数据倍率及分区段描述,表示为:[0066]xsfijk为调理参数,其区间[-10,10][0067](3)无量纲化及归一化处理[0068]对各通道数据分区段除以绝对值xfmax,得到无量纲化数据xfij,i=1,2,3;j=1,2,..,n,表示为:[0069][0070]将无量纲化各通道的切削力描述成数据集形式,表示为:[0071]xf1参数取值范围[-1,1];[0072]xf2参数取值范围[-1,1];[0073]xf3参数取值范围[-1,1];[0074]再进行归一化处理,将xf1j、xf2j、xf3j转化为xcfij=kfm×xfij;其中,kfm是通用数据集中km的一种具体情况,下标f表示切削力,求解过程与km一样,表示倍率系数;[0075]将归一化处理后各通道的切削力描述成数据集形式,表示为:[0076]xcf1参数取值范围[-1,1];[0077]xcf2参数取值范围[-1,1];[0078]xcf3参数取值范围[-1,1];[0079](4)规范化处理后数据的校准[0080][0081]其中,表示规范化处理后的数据,如图3所示为本发明实
施例所述数据校准的过程示意图,通过比较规范化处理后数据与原始数据xfij的误差进行数据校准;[0082]2)针对工作台的振动加速度信号处理过程为:[0083]设有mv个加速度信号通道,用符号xvij描述,加速度单位m/s2,第i通道,i=1,2,3…,mv;第j个数据,j=1,2,3…,n;[0084]针对工作台的振动加速度信号处理过程与切削力信号处理过程相同;[0085]3)针对微位移信号处理过程为:[0086]设有md个微位移信号通道,用xdij描述,单位为mm,第i通道,i=1,2,3…,
瑞士肖布林精密车床 车削中心 车铣磨一体机介绍md;第j个数据,j=1,2,3…,n;[0087]针对微位移信号处理过程与切削力信号处理过程相同;[0088]4)针对机床的功率信号处理过程为:[0089]设有mp个功率参数通道,用xpij描述,单位为w,第i通道,i=1,2,3…,mp;第j个数据,j=1,2,3…,n;[0090]针对机床的功率信号处理过程与切削力信号处理过程相同;[0091]5)针对加工环境的温度信号处理过程为:[0092]设有mt个温度参数通道,用xtij描述,单位℃,第i通道,i=1,2,3…,mt;第j个数据,j=1,2,3…,n;[0093]针对加工环境的温度信号处理过程与切削力信号处理过程相同。[0094]步骤3、再将规范化格式处理后的信号数据通过工业以太网交换机401传输至上位机(即数据库服务器)501,由所述上位机进行数据分析处理,判断所述数控机床的状态或存在的故障。[0095]不同于一般的数据采集系统将数据采集单元与上位机直接连接,本发明实施例在数据采集单元后连接嵌入式系统,由嵌入式系统对同步采集的数据集进行规范化格式处理;然后再通过工业以太网交换机将数据集传输至上位机(数据库服务器)中进行显示与分析;并在上位机完成对数控机床的状态监测后,将监测数据集上传至网络。[0096]值得注意的是,本发明实施例中未作详细描述的内容属于本领域专业技术人员公知的现有技术。[0097]综上所述,本发明实施例所述方法与传统的方法相比,具有如下优点:[0098]1、本发明方法适用于多源传感器同时对多个数据集进行参数感知,确保在数控机床同一工况下采集到所需的多源多种数据集,有利于更准确地监测数控机床的运行状态或发现存在的设备故障;[0099]2、本发明方法利用各类传感器和数据采集装置进行数据采集,由于每个传感器之间都独立进行不同类型数据感知,不存在使用组合式传感器需要对数据进行解耦所带来的难题,保证数据和测试结果的准确性;[0100]3、本发明方法对数据进行的规范化格式处理不同于传统的数据规范化,由于采集不同多源类、不同原理的传感器,所以采集到的数据集在幅值等方面存在差异性,通过本发明提出的方法对数据进行上述方面的规范化格式处理,便于多源信号在上位机中分析处理。[0101]以上所述,仅为本发明较佳的具体实施方式,但本发明的保护范围并不局限于此,任何熟悉本技术领域的技术人员在本发明披露的技术范围内,可轻易想到的变化或替换,都应涵盖在本发明的保护范围之内。因此,本发明的保护范围应该以权利要求书的保护范围为准。本文背景技术部分公开的信息仅仅旨在加深对本发明的总体背景技术的理解,而不应当被视为承认或以任何形式暗示该信息构成已为本领域技术人员所公知的现有技术。
原创文章出自天博,欢迎转载!